News
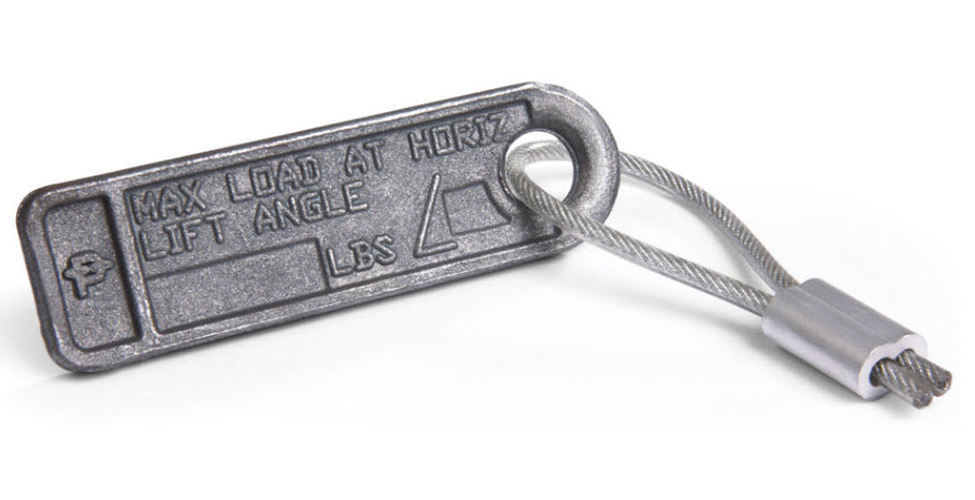
Chain Sling Identification Tag
2021-06-23
Contributed by Bob Kozickie, Technical Sales Support Manager
Edited by Christy Kutchma, Marketing Coordinator
The single most important component on an alloy chain sling is the identification tag. Per OSHA 1910.184, if the ID tag is missing or illegible, the sling must be removed from service. OSHA is diligent in enforcing this regulation. Not only is having the ID tag affixed and legible a requirement, the specific information embossed onto the tag is equally as important. There are seven critical points of data that are required to be on every sling tag.
- Name or Trademark of the Chain Sling Manufacturer – This requirement also applies to any entity that performs a repair on a chain sling. The sling manufacturer is the responsible party for certifying that the chain sling is compliant with all applicable standards. These entities verify, if it is a mechanical chain sling for example, that all components used to construct the sling had been proof tested to twice their working load limit prior to assembly. This is critical information which provides full traceability as to who manufactured or repaired the alloy chain sling.
- Chain Grade – Alloy chain slings can be manufactured from Grade 63, 80, or 100 chain. Each grade has a unique set of characteristics and capacities when used in overhead lifting applications. High heat exposure capacity reduction is one characteristic that is significantly different between the three grades mentioned. Although a single component or the majority of components used to assemble the sling could be all one grade, ultimately the slings’ capacity is established based on the weakest component contained within the sling.
An example would be if a two-leg 9/32” chain sling is assembled with all Grade 100 components but there are 3/8” standard J-Hooks on the bottom. The sling would then be required to marked that it is has a Grade 80 rating based on the fact that all J-Hooks are manufactured using Grade 80 alloy steel and heat treating processes.
- Chain Link Size – Alloy chain is the dominant component used to assemble an alloy chain sling. The chain size is determined by the alloy rod diameter used to form each link. Peerless 1/2”, or 13MM, Grade 100 alloy chain is manufactured from rod with a .529” diameter. Alloy chain size is also used to compile the Chain Sling Capacity Chart used by all riggers when planning and lifting loads.
- Number of Legs or Chain Configuration – The number of legs and the slings configuration are the basis for establishing the lifting capacity. The manufacturers’ choice in selecting the correct master link for 3 and 4 leg chain slings is a major factor of concern with this requirement. Triple and Quad chain slings are required to be assembled onto master-sub assemblies and had to have been proof tested to six times the rated capacity of a single leg chain sling. The chain sling nomenclature acronym can also be used as identification such as SOS, DOS, and TOF.
- Rated Load Capacity at a specified angle – Rated load capacity needs to be identified using at least one specified angle of lift to the load. Single leg slings will obviously be rated at 90° and multiple leg slings are most commonly rated at 60° – which is the angle of greatest capacity and efficiency a multiple leg sling can attain when lifting a load. Some sling manufacturers prefer to make sling tags that show all three angles of lift. Those tags can tend to be extremely large and can oftentimes cause interference when lifting with multiple leg slings.
- Length – The length of an alloy chain sling is measured from the top bearing point to the bowl of the bottom hook. The top bearing point is the point at which the master link connects up to the crane or hoist hook and the bottom point is where the hook or attachment connects to the load. This measurement is documented on the sling tag in feet and inches. Since not all slings will fall exactly on an inch marking, the value is rounded to the nearest inch.
- Unique and Individual Serial Number – The Serial Number is the sequence of numbers or numbers and letters that makes each alloy chain sling distinguishable. When the chains are inspected during annual documented chain inspection, the inspector needs to determine exactly which chains are good and those that meet the criteria for removal. That is accomplished by identifying the chains by their serial number, and tagging those out that are requiring repairs.
Environmental conditions can cause the ID Tag to become illegible. Rust, paint, and grease are some examples that contribute to the inability to read the information. Proper chain sling maintenance requires to keep the tag clean. By coating it with a light oil, you can help to extend the service life and a welders brush can often remove any light rust and other.
The identification tag, with these seven pieces of data, provide critical information to riggers when planning lifts. Understanding why specific information is required to be provided for lifting and rigging equipment is an important part of providing a safe workplace.
Past Articles
Knowing the difference when selecting Grab Hooks
Contributed by Bob Kozickie, Technical Sales Support ManagerEdited by Christy Kutchma, Product & Marketing Associate There are three styles of grab hooks manufactured for overhead lifting: Non-Cradle, Cradle, and Chain Shortening Grab Hooks. Each are designed to shorten, choke, or basket alloy chain slings in a variety of lifting applications. When use...
Trailer Safety Week!
Contributed by Cary Kronebusch, Senior Product Manager Edited by Christy Kutchma, Product & Marketing Associate Welcome to #TrailerSafetyWeek! Peerless is a proud ally of this annual event. Peerless supplies Cargo Control and Trailer Safety Chain Products to the trailer manufacturing industry. As a decades long provider to the industry and a 16 year m...
The Crosby Group to Commence Cash Tender Offer for All Outstanding Shares of KITO CORPORATION
RICHARDSON, Texas, United States, and SHOWA-CHO, Yamanashi, Japan, September 22, 2022 – The Crosby Group, a leading provider of lifting and rigging solutions, and KITO CORPORATION, a leading manufacturer of material handling equipment with 90 years of experience in the development and production of hoists and cranes, today announced that they have secured all regulatory...
The Anatomy of an Alloy Chain Sling Failure
Contributed by Bob Kozickie, Technical Sales Support Manager Alloy steel chain slings are the most durable products used for lifting and rigging. So, why do alloy chain slings fail? Every year we read and hear stories of catastrophic chain sling breaks. When these failures happen, the broken sling components are then sent back to the sling manufacturer or a...
Shall and Should When Reading Regulations
Contributed by Bob Kozickie, Technical Sales Support Manager Governments have established regulations and standards within the workplace in order to provide the highest degree of safety for all employees. These regulations and standards have various degrees of authority depending on whether they are statutory, consensus, or 3rd party documents. When we read...