News
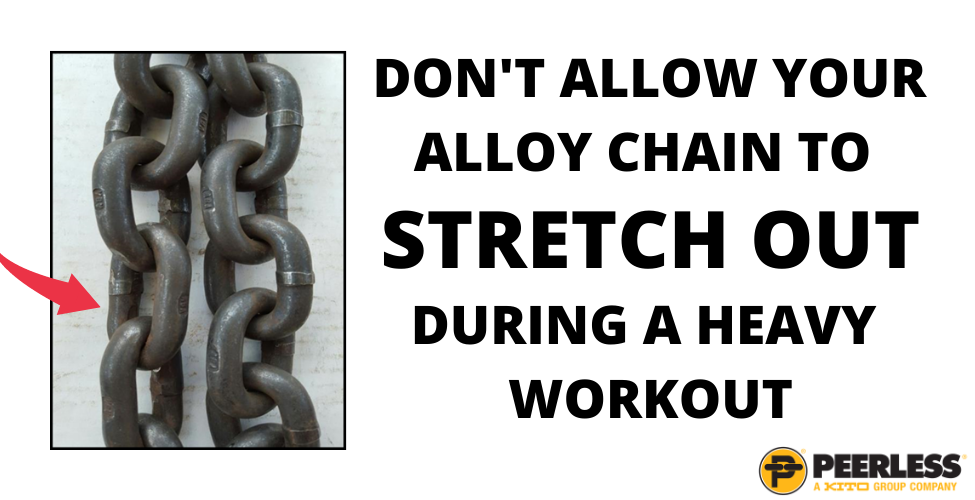
Don't Allow Your Alloy Chain to "Stretch Out" During a Heavy Workout
2021-12-22
Contributed by Bob Kozickie, Technical Sales Support Manager
There are many reasons for selecting alloy chain over wire rope or synthetics for heavy lifting applications. One positive aspect of alloy chain is its strength to weight ratio which provides the durability needed in the toughest environments. Alloy chain is also a very rigid material. This rigidity means that the overall shape of the link must maintain its original form and dimensions throughout its service life.
OSHA mandates that alloy chain slings are to be inspected daily by a competent person as designated by the employer. During the daily and periodic inspections, one criterion required to be verified is elongation of a chain leg or individual links. Alloy chain has no elasticity or stretch when placed under load. Stretch may occur when using other types of sling materials. This is why three and four leg alloy chain slings are rated at the same capacity. One leg will always be a balancing leg while the remaining three legs are carrying the load. This balancing leg will vary from leg to leg as the load is lifted and moved to its designated area.
A very common question posed to chain manufacturers is “How much stretch is allowable in my alloy chain sling leg?” The answer is simple. Any elongation which occurs in alloy chain is criteria for removal. Alloy chain has a minimum elongation of 20% before failure. This is engineered into the chain by using a select combination of different base metals, heat treating, and tempering the chain during the manufacturing process. This is the recipe that gives alloy chain its ductility and strength.
Let’s look at a single link of 3/8” Grade 100 alloy chain. This is the most common alloy chain used for overhead lifting. The nominal inside length, or “pitch”, is 1.23” or about 1-1/4”. Based on the 20% elongation factor, the minimum length at which the chain is designed to fail is 1.47” just short of 1-1/2”. Alloy chain has a characteristic engineered into the link design so that as the inside length increases, the sides will pull into the center creating an hourglass configuration. The link is then designed to break at the ends on the radius area. The radius or “crown” is the weakest area of a single link of chain. The reason for this is simple. A single chain link has two times the chain diameter material, one on each side of the link, and there is only one material diameter on each end. Therefore a single link of chain has a 2:1 ratio of material. When the link does fail such as during a Minimum Break Force Test, the resulting broken link will resemble the number six with the chain pulled in on the sides and the broken radius area open.
Alloy chain is the most durable lifting product available to move heavy loads. Even though alloy chain has all these great attributes, care must be taken to ensure that the chain is not overloaded or shock-loaded while performing its function. Stretching before a good workout may be a good thing for us; it’s not a good thing when it comes to overhead alloy lifting chain.
Past Articles
Knowing the difference when selecting Grab Hooks
Contributed by Bob Kozickie, Technical Sales Support ManagerEdited by Christy Kutchma, Product & Marketing Associate There are three styles of grab hooks manufactured for overhead lifting: Non-Cradle, Cradle, and Chain Shortening Grab Hooks. Each are designed to shorten, choke, or basket alloy chain slings in a variety of lifting applications. When use...
Trailer Safety Week!
Contributed by Cary Kronebusch, Senior Product Manager Edited by Christy Kutchma, Product & Marketing Associate Welcome to #TrailerSafetyWeek! Peerless is a proud ally of this annual event. Peerless supplies Cargo Control and Trailer Safety Chain Products to the trailer manufacturing industry. As a decades long provider to the industry and a 16 year m...
Chain Sling Identification Tag
Contributed by Bob Kozickie, Technical Sales Support Manager Edited by Christy Kutchma, Marketing Coordinator The single most important component on an alloy chain sling is the identification tag. Per OSHA 1910.184, if the ID tag is missing or illegible, the sling must be removed from service. OSHA is diligent in enforcing this regulation. Not only is having the ID t...
The Crosby Group to Commence Cash Tender Offer for All Outstanding Shares of KITO CORPORATION
RICHARDSON, Texas, United States, and SHOWA-CHO, Yamanashi, Japan, September 22, 2022 – The Crosby Group, a leading provider of lifting and rigging solutions, and KITO CORPORATION, a leading manufacturer of material handling equipment with 90 years of experience in the development and production of hoists and cranes, today announced that they have secured all regulatory...
The Anatomy of an Alloy Chain Sling Failure
Contributed by Bob Kozickie, Technical Sales Support Manager Alloy steel chain slings are the most durable products used for lifting and rigging. So, why do alloy chain slings fail? Every year we read and hear stories of catastrophic chain sling breaks. When these failures happen, the broken sling components are then sent back to the sling manufacturer or a...